AWS Weather Station: Real-Time Environmental Monitoring Solution
March 22, 2025 | News | No Comments
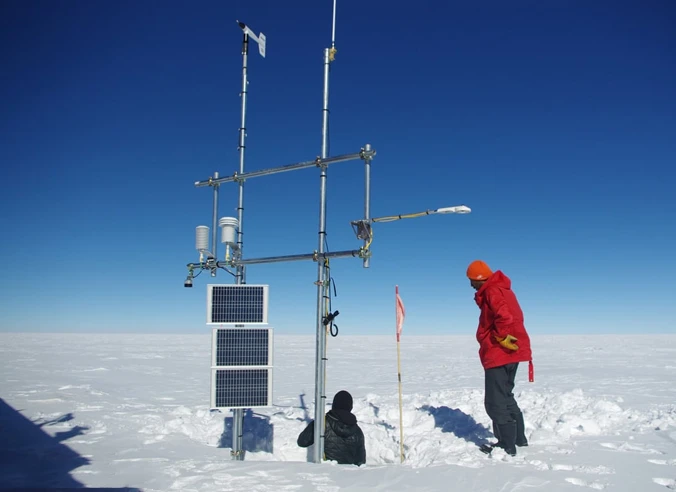
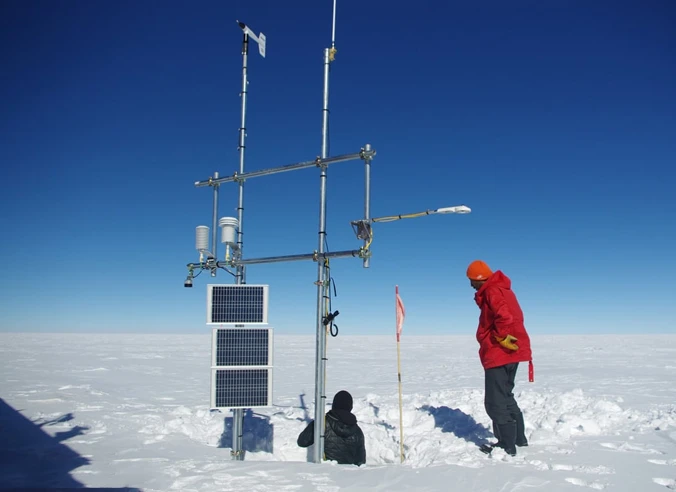
# AWS Weather Station: Real-Time Environmental Monitoring Solution
## Introduction to AWS Weather Station
The AWS Weather Station is a cutting-edge solution designed for real-time environmental monitoring. It leverages the power of Amazon Web Services (AWS) to provide accurate and reliable weather data, making it an essential tool for various industries, including agriculture, construction, and environmental research.
## Key Features of AWS Weather Station
### Real-Time Data Collection
One of the standout features of the AWS Weather Station is its ability to collect real-time data. This ensures that users have access to the most up-to-date information, which is crucial for making informed decisions.
### High Accuracy Sensors
The weather station is equipped with high-accuracy sensors that measure various environmental parameters such as temperature, humidity, wind speed, and precipitation. These sensors are calibrated to provide precise readings, ensuring the reliability of the data collected.
### Cloud Integration
With seamless integration into the AWS cloud, the weather station allows for easy data storage, analysis, and sharing. Users can access their data from anywhere, at any time, making it a highly flexible solution.
## Applications of AWS Weather Station
### Agriculture
In the agricultural sector, the AWS Weather Station can be used to monitor weather conditions that affect crop growth. This data can help farmers optimize irrigation schedules, predict pest outbreaks, and improve overall crop yield.
### Construction
For construction projects, the weather station provides critical data on weather conditions that can impact project timelines and safety. Real-time monitoring helps in planning and mitigating risks associated with adverse weather.
### Environmental Research
Environmental researchers can benefit from the detailed and accurate data provided by the AWS Weather Station. It aids in studying climate patterns, tracking environmental changes, and conducting long-term ecological research.
## Benefits of Using AWS Weather Station
### Cost-Effective
The AWS Weather Station offers a cost-effective solution for real-time environmental monitoring. By leveraging AWS cloud services, users can reduce the costs associated with data storage and analysis.
### Scalability
The system is highly scalable, allowing users to expand their monitoring capabilities as needed. Whether you need to monitor a single location or multiple sites, the AWS Weather Station can accommodate your requirements.
### User-Friendly Interface
The weather station comes with a user-friendly interface that makes it easy to set up and operate. Even users with limited technical expertise can quickly get started with the system.
## Conclusion
The AWS Weather Station is a powerful tool for real-time environmental monitoring. With its high-accuracy sensors, cloud integration, and user-friendly interface, it provides a comprehensive solution for various industries. Whether you are a farmer, construction manager, or environmental researcher, the AWS Weather Station can help you make informed decisions based on accurate and reliable weather data.
Keyword: aws weather station